A lot of big box retailers rely heavily on material handling equipment to keep their warehouses and stores running smoothly. Whether it’s moving products or fulfilling orders, this equipment plays a huge role in day-to-day operations. To make sure it lasts as long as possible, businesses must focus on both facilities asset management and asset life cycle management.
By understanding how to manage equipment correctly from purchase to disposal, companies can save money, improve safety, and reduce downtime.
What Is Asset Life Cycle Management?
Asset life cycle management is all about keeping equipment in good shape throughout its entire lifespan. This includes regular maintenance, upgrades, and knowing when it’s time to replace items.
For businesses that use products like distribution carts or order-picking carts, effective life cycle management helps these assets perform their best for longer.
The Main Stages of Asset Life Cycle Management:
- Acquisition: Buying the right equipment based on your company’s needs.
- Usage and Maintenance: Setting up a regular maintenance schedule to prevent unexpected breakdowns. Checking equipment like industrial carts and fulfillment carts regularly extends their life and improves safety.
- End of Life: When equipment becomes outdated or inefficient, it’s time to replace it. Properly disposing of or recycling equipment can also save money.
Managing these stages well helps companies cut costs and avoid costly equipment failures.
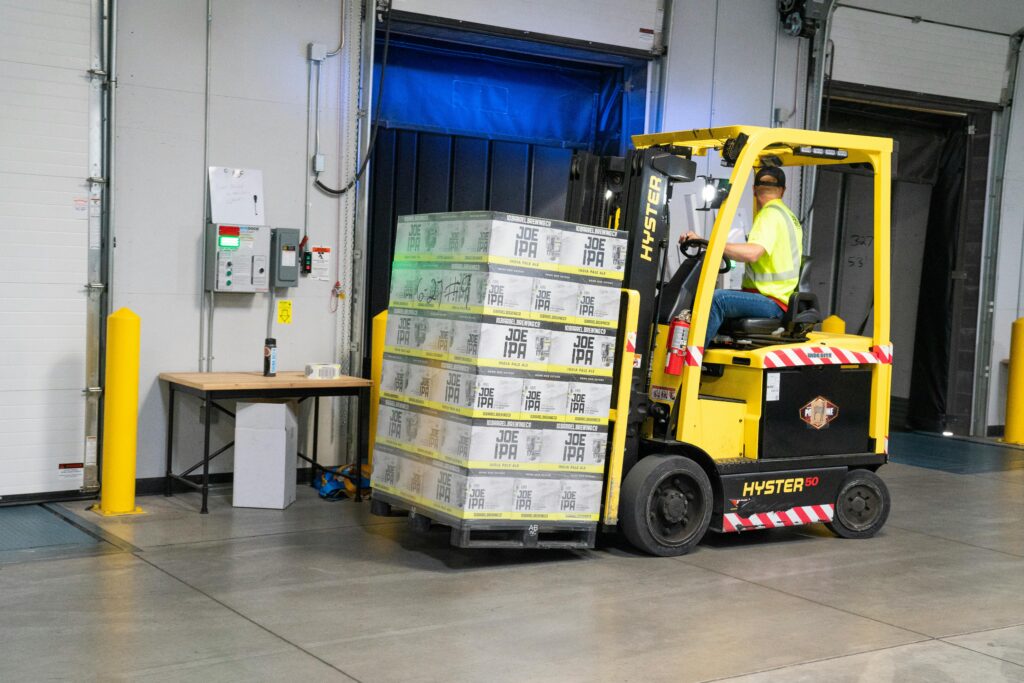
Facilities Asset Management: Keeping Operations Smooth
Facilities asset management is about maintaining all the assets within a store or warehouse, not just equipment. This includes everything from ladder carts to forklifts. Good management ensures that all assets are in working condition and helps prevent delays or safety risks.
For large retailers, managing thousands of products a day requires well-maintained material handling equipment. A strong facilities management plan helps businesses schedule maintenance during slow times, which keeps operations running smoothly.
Benefits of Effective Facilities Asset Management:
- Extends the life of equipment.
- Cuts down on repair and replacement costs.
- Improves safety and operational efficiency.
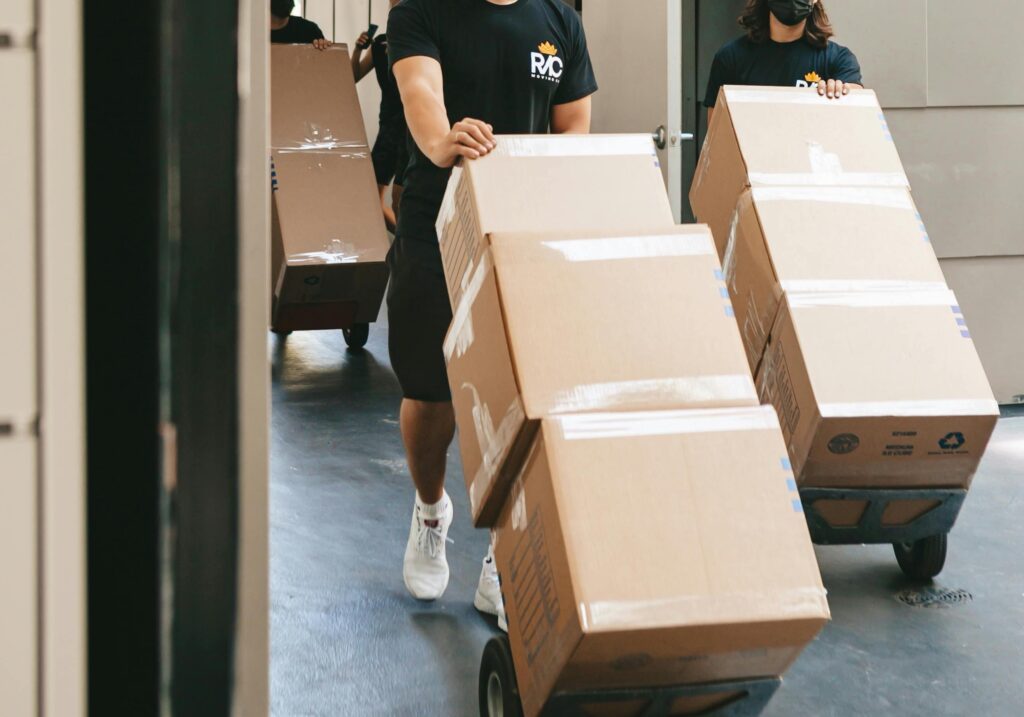
National Cart: Your Partner in Material Handling Equipment
Having the right equipment partner is crucial. National Cart offers high-quality material handling products that are built to last. From warehouse equipment to customized solutions, we help businesses like yours stay efficient and safe. Our durable products fit perfectly into any facilities asset management or asset life cycle management plan.
By focusing on asset life cycle management and investing in high-quality equipment like National Cart’s products, your business can run smoothly while reducing costs and avoiding downtime.
For more tips on protecting your equipment, check out our related article on Hurricane Season Prep for Material Handling and Warehouse Equipment.